A New Industrial Revolution is Already Underway
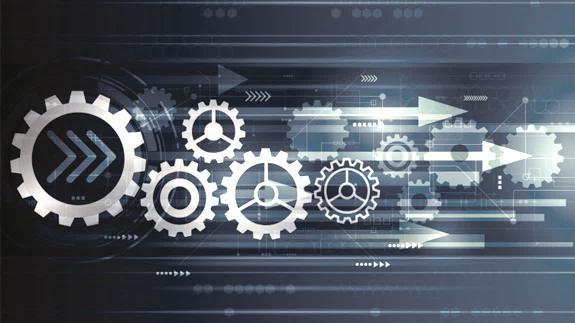
For many years, Manufacturers pointed to pricing and margin compression as their top overall business concerns. In today’s growing economy, although pricing and margin compression continue to concern some, many of these same Manufacturers point to a skilled workforce shortage and limited capacity as their top business overall concerns. These same Manufacturers also see “speed” as a growing need in today’s technologically advanced setting. To address these new concerns, Manufacturers are focused on automation and technology as sustainable and scalable solutions to workforce shortage, capacity and “speed”. This “smart manufacturing,” phenomenon is creating a host of opportunities for those manufacturers willing to change.
In a competitive economy, the company that is fastest at closing the sale is the winner. However, a big bottleneck in getting that closed deal comes in at the quoting stage. Studies indicate Sales personal spend more than 25% of their time on administrative tasks. In companies that engineer or configure to order these studies show that 50% of the engineering staffs time is allocated to administrative tasks. And often when the order is received many of these tasks are duplicated. And let’s not forget that there can be human errors in creating quotes or the time it takes to chase down a sales manager to get an approval on a discount or lower price. All these administrative costs and policies slow progress while reducing the probability of a sale and the profitability of the company. This is exactly why Manufacturing companies today are experiencing a new trajectory in which eCommerce, EDI, auto-loading from Web-based MRP, Product Configurators and CAD integration tools are rapidly growing. This growth is facilitating a shift away from the more typical B2C (business-to-consumer) sales toward a B2B (business-to-business) sale. This is particularly true for those Manufacturers involved in aerospace, defense, medical and automotive industries. However, regardless of the industry, eCommerce, Product Configurators and CAD integration tools are no longer a nice to have, but rather a need to have for most manufacturers.
On the shop floor the traditional people driven, batch manufacturing that depended on tribal knowledge, off-line scheduling schemes and detached supply chains are quickly being replaced. A look at today’s “smart manufacturing” shop floor shows advanced companies are going Lean, establishing process driven signals and working to deploy interconnected system of machines, inspection equipment and business tools (ERP, QMS, CAD, CAM, CRM, etc.) to overcome workforce shortages and real or perceived capacity constraints. Multi-Task turning and 5-axis milling machine solutions now work for any manufacturing or volume requirement by reducing and in some instances eliminating setup while providing manufacturers with the ability to run lights out. Integrated CMM and metrology tools now allow for fast, in-line inspection that eliminates time consuming set up and eradicates those onetime bottlenecks in your Quality department. By dramatically increasing “speed” Manufacturers are increasing productivity and throughput while decreasing downtime. This “smart manufacturing,” phenomenon is also driving machine reliability, performance and customer on-time delivery to new levels.
With the improvements to the front office and shop floor through “smart manufacturing” the need for smart, effective tools for managing purchase orders and suppliers is more evident. Supplier portals that integrate with ERP systems allow companies to communicate with suppliers faster. Manufacturers have now closed the Supply Chain loop by connecting the complete supply chain (customer to production and production to vendor) via system integration to enable pull systems to flow seamlessly and with the least amount of non-value added administration. This is leading to cost and lead-time reductions while increasing profitability and customer satisfaction. Through this interconnected “smart manufacturing” approach Manufacturers can accurately predict inventory levels, customer deliveries and the all-important, but sometimes overlooked, actual cost gross margin by order line and product. All of which are essential to the success of today’s Manufacturer.
Inventory and shipment automation are providing some of the greatest gains in overall efficiency and quality. Prior to the “smart manufacturing” industrial revolution inventory and shipping data was manually entered into computers, while warehouse and stock room workers were kept busy putting stock away or picking parts for production and customer orders. The lack of real-time information about stock on hand made it difficult to support production or provide good customer service. And accuracy issues often lead to stock-outs, missed or wrong shipments and added non-value added costs and activities. These conditions are changing rapidly in manufacturing today. In an automated warehouse or stock room, all items are scanned as they move in, out, and around the facility. The scanned data is downloaded directly to the ERP system to provide real-time information about the products location. When an order comes in, the customer service need only access the computer records to see how much of any given product is in the warehouse or stockroom to accurately pinpoint where it is located or when it will be ready for shipment. In the past, these sophisticated warehouse systems were expensive, difficult to deploy and built for the fortune 500 companies. Fortunately, today Manufacturers can deploy only the level of automation needed to satisfy their business requirements. From semi-automated to fully automated and everything in between, these systems are far more adaptive, less expensive, easier to deploy and can be fully integrated into your ERP system to provide the greatest return on the investment.
While the competitive advantages are clear, some manufacturers are slow to digitize their operations because they’re unaware of the technologies available to them or are concerned about the required time, cost and infrastructure investments. However, it is clear to those close to the manufacturing sector the new industrial revolution is already underway. Manufacturers struggling to maintain and even expand the use of legacy and homegrown systems will be left behind and unable to adapt to the latest applications and platforms. What some see as a disruptive force (smart manufacturing) is really a solution that is already underway. And it is a phenomenon that is creating an opportunity for those manufacturers that have jumped on board.
Don’t be left behind!
Authored by: Michael P. Canty
Synergy Resources, Business Unit Director
Strategic Business Services