PFM: A Next Generation Production Control System
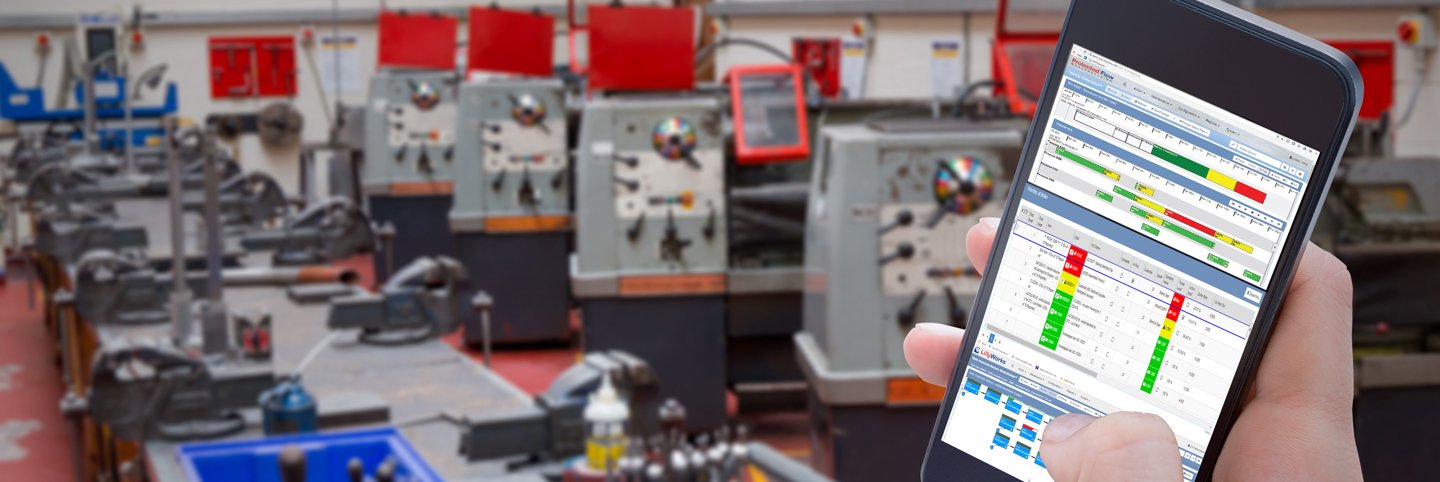
If you recall, in part one of our series on production control, we talked about the evolution of production control systems, with special attention to what makes shop floor scheduling using traditional solutions so challenging. Then, in part two, we discussed the different features and capabilities that a scheduling system must possess in order to be considered truly advanced.
In our mission for continuous innovation, Synergy Resources has had the opportunity to partner with different companies that are redefining the production control landscape; LillyWorks is one such company. Dick Lilly, founder of LillyWorks, has been pioneering scheduling and material planning software since 1960. Lilly, a close associate of business management guru Eli Goldratt, earned acclaim for developing VISUAL Manufacturing, an enterprise resource planning (ERP) solution that leverages Goldratt’s theory of constraints model.
In 2016, Dick Lilly and his sons Mike and Mark set out to develop a next generation production control system, called Protected Flow Manufacturing (PFM).
PFM takes an entirely new approach to production control and meets the criteria identified in our second post. It:
- Is intuitive and easy to use
- Anticipates change and adjusts to it in real time
- Prioritizes resources to achieve the best outcomes for all work orders (WOs)
- Self-expedites
- Doesn’t require a high level of data input or maintenance
- Automatically aligns dependent WO dates with top-level demand
- Provides users with the information they need to execute work now and plan for the future
PFM is Intuitive & Easy to Use
Unlike traditional ERP finite capacity scheduling systems, which use complex algorithms to calculate WO priorities based on load and capacity data, PFM makes it easy to understand how work is prioritized on the shop floor.
Simply put, PFM identifies a WO’s “threat level” — that is, its risk of being late. PFM presents each WO’s threat level as a value (the higher the number, the greater the risk), as well as color codes it (red, yellow, green) on all output displays, including work center displays and electronic visual dashboards within the factory.
PFM calculates prioritization in real time, eliminating the need to rerun an obsolete schedule. According to the PFM customers we’ve spoken to, they’ve found it to be the first time that the entire shop floor trusted a schedule and worked to it.
PFM Anticipates Change & Adjusts to It in Real Time
Most modern finite scheduling systems generate precise schedules, which shop floors are expected to follow to the letter. The issue with this is that it doesn’t account for variability; when something happens unexpectedly, the system is incapable of dynamically adjusting schedules. Instead, it simply reruns the schedule over and over again.
By comparison, PFM operates on the principle that something will inevitably go wrong on the shop floor. To that end, it solves for variability by enabling you to assign a “time buffer” to each WO; this time buffer protects the WO from unexpected variables on the shop floor, such as issues with people, machinery, and materials or even just customer changes.
Based on the reliability of resources, people, suppliers, and materials, as well as how much variability you typically experience, PFM dynamically assigns buffers to WOs. This eliminates any need for a high level of data accuracy and schedule maintenance.
Once PFM has assigned a time buffer to a WO, it automatically monitors the size of this time buffers in real time. If a WO’s time buffer shrinks — say, from 12 hours to eight — PFM will recognize that the WO is losing its protection and that its threat level has increased. Based on this information, PFM will dynamically adjust that WO’s priority. In this way, PFM is able to anticipate problems and protected WOs as they flow through the shop floor.
PFM Prioritizes Resources to Achieve the Best Outcomes for All WOs
Building on the concept of the use of a time buffer, one of the things that makes PFM so advanced is its prioritization methodology: To determine a WO’s threat level, PFM divides the total amount of time left on the WO (% Work Remaining) by the total amount of time left to complete the WO, known as the “buffer” (% Buffer Remaining).
Based on this equation, if a WO had 30% of work remaining and 50% of buffer left, its threat level would be 0.6. If a WO had 80% of work remaining and 20% of buffer left, its threat level would be 4.0. The higher the threat level, the higher its priority. Therefore, a WO with a 4.0 threat level should be prioritized over a WO with a 0.6 threat level.
PFM prioritizes WOs in real time as work is (or isn’t) being completed. Unlike traditional finite capacity scheduling systems, which produce pre-generated schedules, PFM automatically changes priorities as soon as it detects a change in the WO’s status, all in real time, right on screen.
Rather than schedule WOs one at a time and load them into the shop floor capacity, which essentially locks up that capacity from the next WO, PFM identifies the threat level of each WO at the time it reaches a resource. Based on that information, PFM determines which WO to work on next. In doing so, PFM “balances” the use of resources to create the best possible outcome for all WOs.
PFM also includes a powerful feature called “Control Points.” Every production cycle consists of multiple steps. Each of these steps has various points within it that need to be monitored for completion, such as when the job is released, when an operation must go for outside service, when two or more work orders must converge so that their parts can be assembled, and so on. Using PFM, you can establish control points at each of these process points and assign them buffers. To that end, the Control Points feature enables you to see whether a process is in danger of being completed within the buffer and is, essentially, out of control.
PFM Self-expedites
Because PFM calculates threat levels in real time, it doesn’t require manual expediting; instead, the passage of time and completion of work automatically raise or lower a WO’s threat level. PFM inherently knows which WOs pose the highest risk of not being completed on time and moves them up the dispatch list for the resource in question.
For example, if WO #1 has a problem with the tooling at a machine and sits waiting for a new tool, its threat level will rise in real time as its percent of remaining buffer declines. Conversely, if work is completed faster than expected on WO #2 at its current operation, its threat level will go down because the percent of remaining work has decreased.
PFM Doesn’t Require a High Level of Data Input or Maintenance
As we discussed in part one of this series, finite capacity schedulers will not work unless run time, capacity levels, and work completion are all at least 90% accurate. By comparison, PFM is far less sensitive.
In fact, PFM can operate without run times at all, though using run time data does help it work better. Even if your run time data is inaccurate, PFM enables you to define buffers at the resource level. As a result, if you know that one or more of your resources are difficult to estimate, you can add more buffer to that resource.
We’ve seen manufacturers take months to start using a scheduling system due to poor data accuracy; with PFM, you can implement a prioritization system within a matter of days or weeks because there is no need for rigorous setup or data maintenance.
PFM Automatically Aligns Dependent WO Dates with Top-level Demand
Using a feature called “Elastic Due Dates,” PFM uses logic to understand the dependency of each WO and adjust their due dates any time a top-level dependency changes. This eliminates the need for planners to manually make changes to WO due dates. PFM may just be the only solution on the market capable of doing this.
PFM Provides Users with the Information to Execute Work Now & Plan for the Future
PFM leverages a predictive analytics model called the “Predictor,” which simulates the threat level prioritization method for every WO in the system. Once the simulation is complete, the Predictor provides data-driven insights into which WOs will be late, why they will be late, and what capacity changes need to be made in order to mitigate any late WOs. By providing a window into the future, the Predictor enables manufacturers to make more informed business decisions in both the short and long term.
Reimagine Production Control with PFM & Synergy Resources
As you can see, PFM fundamentally changes the way shop floors approach scheduling and reimagines production control. Though the idea of not using spreadsheets or rerunning schedules might seem foreign to manufacturers who are accustomed to finite capacity-based systems, PFM customers can attest that letting go of the past and stepping outside of your comfort zone are key parts of implementing a next generation system.
Synergy Resources is both happy to see new developments in the field of production control and excited to be a part of that progress. We’ve helped over 800 customers achieve their full potential in all areas of manufacturing and business performance, and we fully intend to continue to help our clients find solutions that improve their ability to meet customer commitments.
Contact us today to find out how Synergy Resources can help you reimagine production control.