Why Manufacturing should end its Love Affair with the Crystal Ball
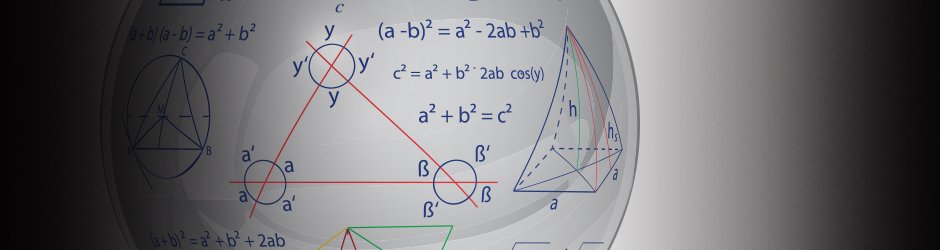
Our Fascination with Predicting the Future
Some say that the definition of insanity is doing the same hurtful thing over and over and expecting different results. If so, then driving actual production from a forecast is insane. Since the dawn of time (back in the 1960’s when dinosaurs roamed the earth), manufacturing software systems have used forecasting and master scheduling to drive actual production of standard and semi-standard products. Today companies still use this approach and continue to carry excess inventory, experience stock outs and miss deliveries. I will not deny that the introduction of this approach was an improvement in the 1960’s but surely we can do better today than live with the drawbacks of a 50-year old methodology.
Good S&OP discipline calls for the creation of a forecast as a target but a forecast is, at best, a guess of what customers are going to buy and when they are going to buy it. It is always going to be wrong. Customers will always buy more of some items and fewer of others than was forecast. Even when they buy the quantity that was predicted, they invariably do it sooner or later than was predicted. Driving production to meet this forecast is operating under a false assumption.
To make matters worse, there’s yet another false assumption: standard lead times used in the production planning process. That seemingly harmless little data field on the part master that supposedly represents the amount of time it takes to manufacture an item from its components. The amount of time it takes to make something is variable. It depends on a lot of factors like load against capacity, amount of variability in the process, dependability of suppliers and phase of the moon.
ERP systems combine the false assumptions of forecast accuracy and standard lead times to create a production plan that from the very beginning has a very slim chance of meeting actual demand. Since meeting actual demand is what we actually get paid to do, we should be concerned about this. Is that what the folks in development at your ERP software company are busy working on improving? I doubt it. Ask your software rep and he or she will tell you about the latest tool to come up with a better forecast or about “the cloud”. He or she may not even understand what you are talking about.
There is a better way, one that challenges the assumptions that were made by my father and the team at IBM that created the Production and Inventory Control (PICS) model at IBM in the 1960’s which served as the blueprint for what APICS has taught for decades. My next blog post will begin to explain this approach. If you can’t wait until then,
click here to find out more!
Who is Mike Lilly?: Mike Lilly is an expert at improving the delivery performance of Manufacturing companies by applying industry best practices – TOC, Lean, SixSigma, the right software tools, and results-driven professional services. Companies Mike works with typically see dramatic improvements in their ability to deliver on-time to their customers, along with the resultant effects of lower WIP, Raw and/or Finished Inventory, and plenty of freed up cash.