Struggling with Production Scheduling? There is a Better Way.
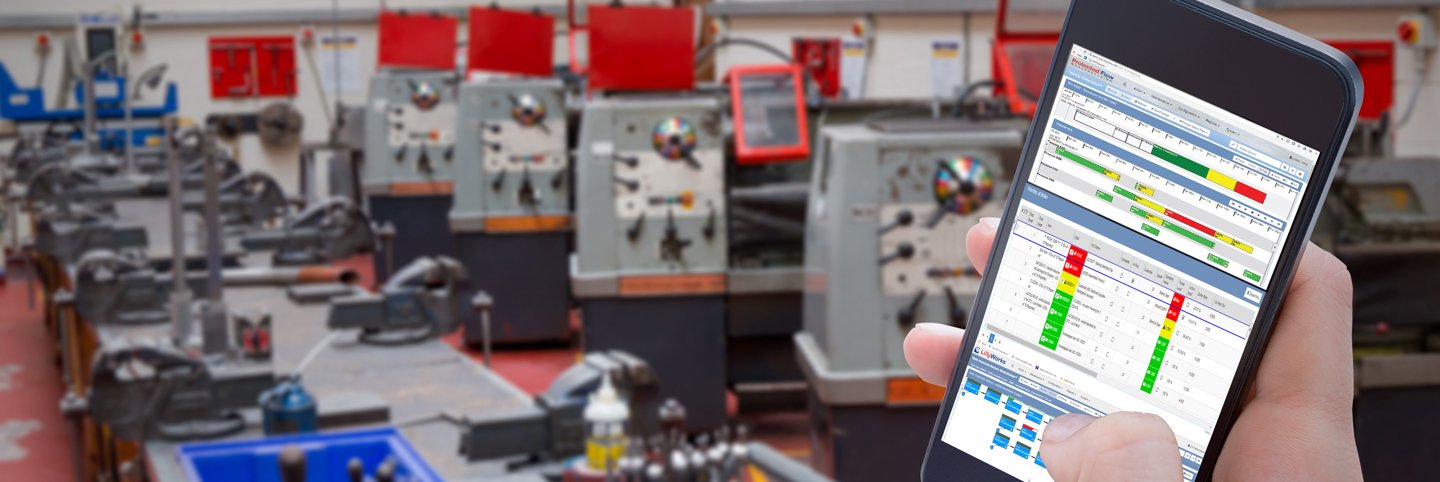
For Job Shop Manufacturers, Production Scheduling is a Notoriously Thorny Problem…
Complex bills of materials, setup and tooling requirements, sub-assembly requirements, and unpredictable delivery dates often wreak havoc on production schedules. Workers call in sick, machines go down, and priorities can change on a dime. When customers call for orders to be expedited (as they inevitably do), it forces a frenzied re-prioritization that can have a domino effect on virtually every aspect of shop floor management.
Traditional shop floor scheduling is built upon a decades-old paradigm: take the order, plan the work, then execute. In a world where nothing changes and nothing goes wrong, that model might work reasonably well. Unfortunately, we all know that it just doesn’t align with reality. Things change, and when they do, everything on the shop floor must adjust to that change.
In practice, today’s traditional scheduling software attempts to solve these issues by forcing you into a never-ending process of re-configuring the schedule, adjusting for unexpected circumstances, and shifting priorities. That’s tremendously time-consuming, and it can be difficult, – if not impossible, – to get things just right. Ultimately, this leads to delayed deliveries, increased costs to expedite shipments, wasted time, and dissatisfied customers. Fortunately, there is a better way.
A Better Way of Production Scheduling
The solution to why manufacturers struggle with traditional scheduling software isn’t different traditional scheduling software; it lies in a different approach to scheduling altogether. The old paradigm tells you to take a customer’s order, plan the job, and complete the work order. As we noted earlier, that only works as long as nothing changes.
A better approach is to build flexibility and adaptability into work order scheduling. This can be accomplished using predictive analytics that recalculate requirements automatically as required delivery dates change. Not only must the work orders for finished goods be adjusted to meet the new targets, – the dates for all components within the bill of materials must likewise be recalculated. That includes subassemblies and the work orders that drive their production.
That’s an adaptive, responsive approach. By automating that process, manufacturers can quickly adjust to changes whenever they happen (which they inevitably will). Instead of spending hours poring over work orders, assessing resource requirements, and reconfiguring production schedules; shop floor managers can simply run “what if” scenarios based on proposed changes, accept or reject the new delivery dates, and recalculate work order schedules automatically.
It’s not just delivery dates that can change. When unexpected resource constraints emerge, – such as a machine going down or a worker calling in sick,– production schedules must be adjusted to keep things on track. With adaptive scheduling built around modern predictive analytics, that process can be automated.
This automation eliminates the guesswork that’s typically associated with production scheduling. When customers call to ask about expediting an order, management can provide answers quickly, and with confidence. Instead of constantly struggling with the question of which job to work on next, managers can easily identify priorities and move on to the next task at hand. Visibility to shop floor operations is vastly improved, and work-in-process can be substantially reduced. On-time deliveries improve dramatically.
Protected Flow Manufacturing (PFM) offers a flexible, adaptable platform for production scheduling that integrates with your existing ERP system. PFM is built on the premise that in most manufacturing companies, things will inevitably change, – whether that’s a customer request for early delivery, delayed receipt of incoming materials, or a machine that’s down for a day or two.
PFM uses predictive analytics to help you stay ahead of all these changes, pivot quickly, and remain agile. Customers that implement PFM typically achieve on-time delivery rates of 98% or better within months of implementing the software.
Get the Details: How Can PFM Help Your Business?
Synergy Resources has put together a collection of short videos that explore the fundamental challenges of production scheduling and describe how our Protected Flow Manufacturing (PFM) solution addresses those challenges in a fundamentally new and different way. Here’s a preview:
Challenges of Production Scheduling provides a brief overview of the problem. Why doesn’t the traditional method of production scheduling work? What are the advantages of a new approach, and how does PFM address that?
Controlling WIP explores the question of whether it makes sense to get orders into the production queue as soon as possible. It sounds like a good idea, but is it really the most efficient way of doing things? By aligning production schedules with available resources and priorities, PFM helps shop floor managers to identify what needs to be done, and in what order, to maximize overall efficiency.
The Work Order Status Board shows how PFM can provide you with real-time visibility to materials availability, throughout the entire BoM structure, including subassemblies. PFM’s Work Order Status Board helps managers to quickly and easily identify potential gaps and make the necessary adjustments so that production stays on track.
Shop Floor Visibility explores how PFM shows you where your jobs are in the production process and how much time is left to complete them for your customers. That gives you accurate answers to important questions about timing of deliveries and the feasibility of expediting orders for your customers.
Game Plans shows you what your available production capacity looks like, and which constraints are bottlenecks could affect the timing of or orders. That allows you to plan now for machine constraints or human resources capacity constraints so that product gets delivered on time.
Get Started Fixing Your Scheduling Problems Today
Incorporating Protected Flow Manufacturing into your existing manufacturing environment is easy. PFM integrates seamlessly with your current manufacturing ERP system, providing a coherent, unified user experience. If your company is struggling to manage the complexities of production scheduling, if your record of on-time deliveries is not what you would like it to be, or if you struggle with limited visibility to shop floor operations; you owe it to yourself and your staff to take a look at PFM. With it, you can confidently respond to customer requests, make realistic promises, and meet your commitments on time.
We encourage you to explore the videos linked above, and contact us to arrange a one-on-one demo of Protected Flow Manufacturing. Or watch our on-demand demo right now to learn more.