Productivity and performance are top priorities for every manufacturer. With effective systems and processes, they don’t have to be competing goals. Infor Quality Management (IQM) introduces control and consistency to the product lifecycle and supply management, so you can bring high quality goods to the market faster.
Fully integrated total quality management.
Continuous improvement starts with strong knowledge management. With IQM, you can consolidate data into a single, unified quality management system (QMS), eliminating duplicate data entries and ensuring compliance in the process. Using IQM’s built-in analytics and reporting tools, you can pull data from purchase and work orders and gain valuable insight into how to reduce defects and drive continuous improvement through statistical process control (SPC).
Wide-ranging support for industry standards.
IQM supports numerous industry standards, including: ISO 9001:2015, AS9100 and AS9102 for the aerospace industry. ISO 13485, CGMP, and FDA Title 21 CFR Part 11 for the medical device industry. MIL-I-45208 and MIL-Q-9858 for military QA systems and ISO/TS 16949 for the automotive industry.
Reduce quality costs to increase profits.
Poor quality costs directly affect organizational profit margins. If negative quality trends go undetected, the costs of goods sold (COGS) will increase while earnings decrease. With IQM, you can reverse these trends, which reduces COGS while dramatically increasing revenue.
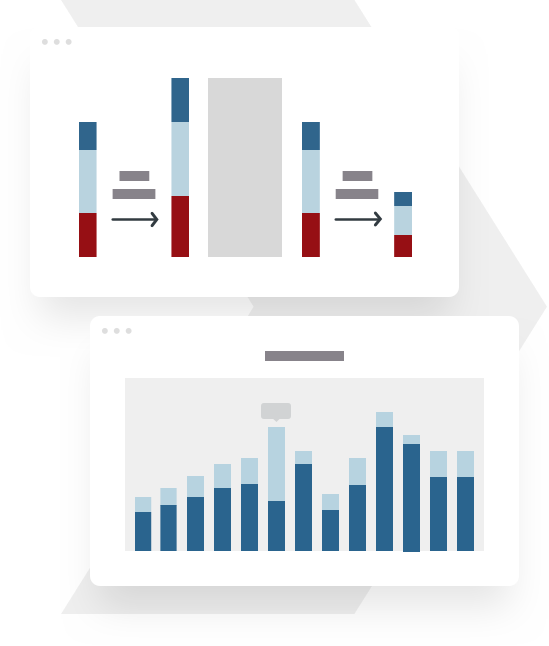
A Comprehensive Quality Solution.
-
16 Quality modules in one comprehensive Quality System
1. Supplier Management
2. Customer Management
3. Employee Management
4. Document Management
5. Product Documentation
6. Process Management
7. Preventive Maintenance
8. Calibration Management
9. Inspect/Data Collection
10. Statistical Process Control
11. Nonconformance Management
12. Corrective Action Preventive Action (CAPA)
13. Advanced Product Quality Planning
14. Production Part Approval Process
15. Cost of Quality
16. Audit Management
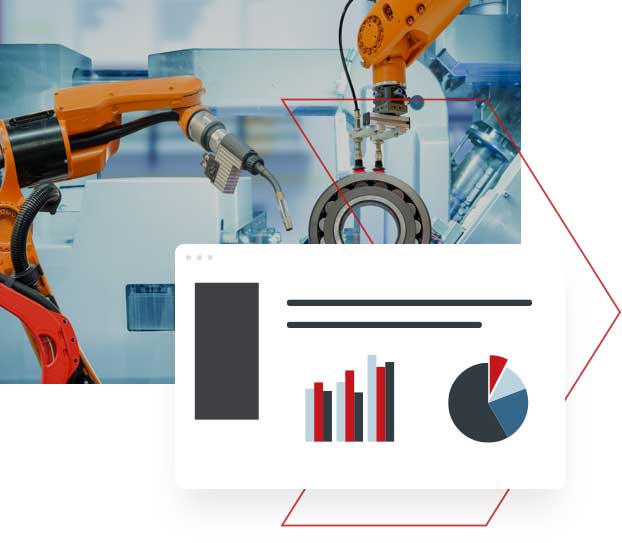
Cradle to Grave Traceability
Never again find yourself wasting time searching through copious amounts of quality records for information. IQM automatically links defects identified during inspection to nonconformance and corrective actions for streamlined quality control. IQM also makes it easy to electronically collect approval signatures, search for data records through available fields, and locate detailed employee training and certification records.
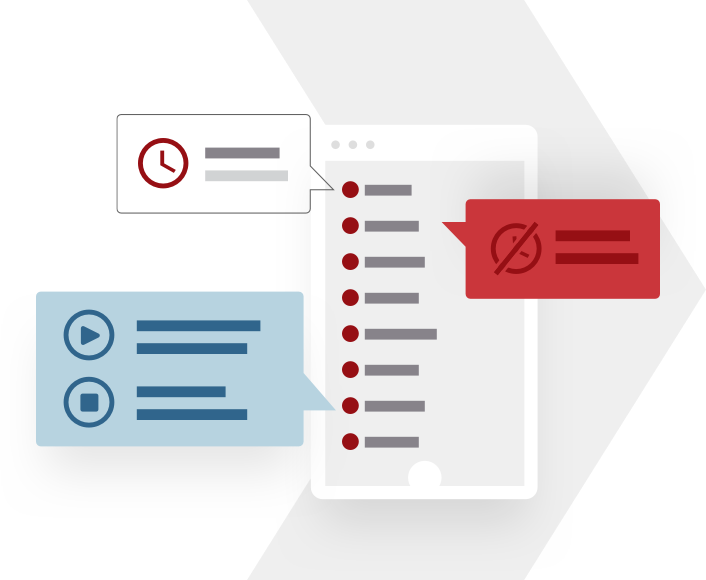
Analytics & Reporting Tools
- Analyze defect data by occurrence, quantity, cost of quality, and more
- Kick off corrective action and continuous improvement projects based on data trends to simultaneously improve quality and customer satisfaction and boost profits
- Utilize SPC data to see when processes are out of control and whether immediate intervention is necessary