Protected Flow Manufacturing™ resolves on-time delivery challenges in high-mix manufacturing environments, turning due dates from guesses to solid commitments. Now, manufacturers can capture more business, charge a premium for shorter lead times, and reduce the time between paying for materials and collecting from customers.
PFM provides the visibility and control to achieve 90-100% OTD without added capacity or heroic efforts.
Protect Commitments to Customers
PFM lets you make due date promises with confidence. With real-time visibility on changing threat levels (the risk of jobs being late), your team can pivot to keep jobs on track.
Make Shop Floor Scheduling Easy
PFM provides a clear priority for each operation, without complex finite scheduling. Rather than trying to plan (or guess) the use of each resource into future time periods, PFM dynamically prioritizes every work order in real time for optimal productivity and on-time delivery.
Bring Scheduling and Visibility to Any ERP
PFM seamlessly integrates with your existing ERP, providing complete transparency between financial performance and production.
Increase Profitability for Manufacturing
By giving you a competitive edge with shorter lead times and consistent OTD, PFM helps you sell more to existing and new customers at prices that improve your profit margins.
Get Answers for Shop Floor Execution
With PFM, you will always know the answers to critical questions like, “What should we work on now?” and “What should we work on next?” Even more important, you will be able to tell customers with confidence when they will get their orders, knowing the delivery dates are solid.
Anticipate Issues and Adjust Accordingly
Other manufacturing scheduling tools assume that everything will go as planned. These plans quickly become out-of-date when “stuff” happens. PFM knows the unexpected will occur and dynamically adjusts resource assignments in real time to head off problems. The most current, accurate information is always in the hands of the people that need it. Job assignments are understood, trusted, and completed in the right order.
Optimize Large & Small Jobs
The traditional approach scheduling prioritizes work orders by due date. PFM looks at due date and job duration to ensure that longer jobs are started at the right time (even if that means starting before shorter jobs that are due sooner). This approach optimizes resources across all jobs to avoid lateness.
Stop the Constant Crisis of Rush Jobs
Expediting jobs is time consuming, costly, disruptive, and stressful for your team. PFM reduces the amount of “hot jobs” by monitoring work completed across all jobs in real time and reprioritizing automatically to keep all jobs on track for OTD.
Connect with Your Manufacturing ERP
PFM can seamlessly be integrated or embedded directly into your existing manufacturing ERP system to augment and extend its functionality. If you don’t yet have an ERP, PFM can serve as a standalone scheduling platform.
Enjoy Easy Setup and Maintenance
Traditional planning and scheduling software requires extremely high data accuracy and constant data maintenance to work. PFM makes things much simpler, allowing you to gain visibility on the status of every job and begin improving on-time delivery in a matter of days.
Solve the Late Problem in Manufacturing…for Good!
We implemented Protected Flow Manufacturing (PFM) to help manage our busy production floor by prioritizing jobs and directing the flow of WIP from department to department. Our implementation took only three months and both our management team and employees immediately saw results. It was like a light switch was turned on - overnight our 13 separate departments became one unified factory, working in unison and harmony to achieve our end goals! PFM is the exact tool we needed to ensure everything is done on time while eliminating any human error. Once PFM was implemented, we saw 100% improvement in our work environment.
We implemented Protected Flow Manufacturing (PFM) in 2017 for its Demand Driven Material Requirements Planning (DDMRP) functionality and the surrounding features of LillyWorks. PFM suited our Enterprise Resource Planning (ERP) needs. PFM is a great all-around fit for our company. Our biggest concern was our raw material supply chain management and as a mature startup, we are aggressively growing which means things change for us rapidly. The DDMRP component and the way that PFM handles the order points and buffers in real-time, on the fly, is exactly what we need. We import our customer forecasts and utilize the historical demand which resizes our buffers automatically; order points are magically moved as needed and safety stock is handled perfectly by PFM every time without issues. PFM supports our rapidly growing company and is worth it! My advice to any manufacturer looking at PFM would be to get educated on DDMRP, compare it to traditional MRP, and once you have determined it is the right fit for your company, go with LillyWorks PFM.
Since implementing Protected Flow Manufacturing, our Throughput is up by about 250% and I can account that to the ability to get the data and make the right decisions.
The results were immediate. We went from four weeks late to three weeks late to two weeks late to one week late. And now, I can look out one month and see that we’re going to be one day, two days late on this job, but on time for that job.
We don’t "kick" all of the jobs to the shop floor at once like we used to. Putting too many jobs onto the shop floor prematurely burns up machine time. You utilize capacity before it needs to be used by putting all the jobs out on the shop floor at once.
In the first couple months using PFM, our concentration was to just get rid of the backlog of late orders. Now, since February 2018, we’ve run four months in a row where we’ve been 90% or better on time with all of the orders coming through the door. That’s a dramatic turnaround!
Our team has been wanting something like PFM for a long time. Our production scheduler, in particular, was tired of just winging it. We fought with on-time-delivery for most of last year. Now we’re exactly where we want to be, operating much more efficiently and consistently getting jobs out the door on time.
PFM's Uses the 3 Performance Principles of the Dynamic Production Method
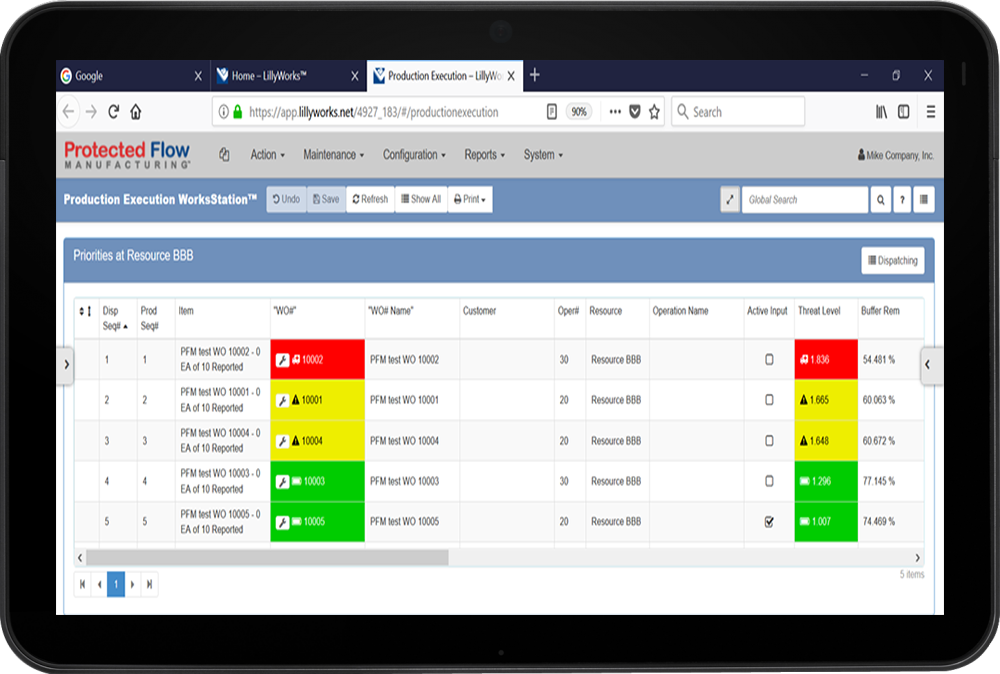
Pragmatic Planning with Flexible Time Protection
Nothing ever goes exactly as planned in Production. Now, you don’t have to recreate a production schedule when that happens. Appropriate buffers are built into each job to provide an early warning and room for adjustment. As the buffer is used up and the risk of lateness increases, PFM automatically reprioritizes tasks in real time to support OTD across all jobs.
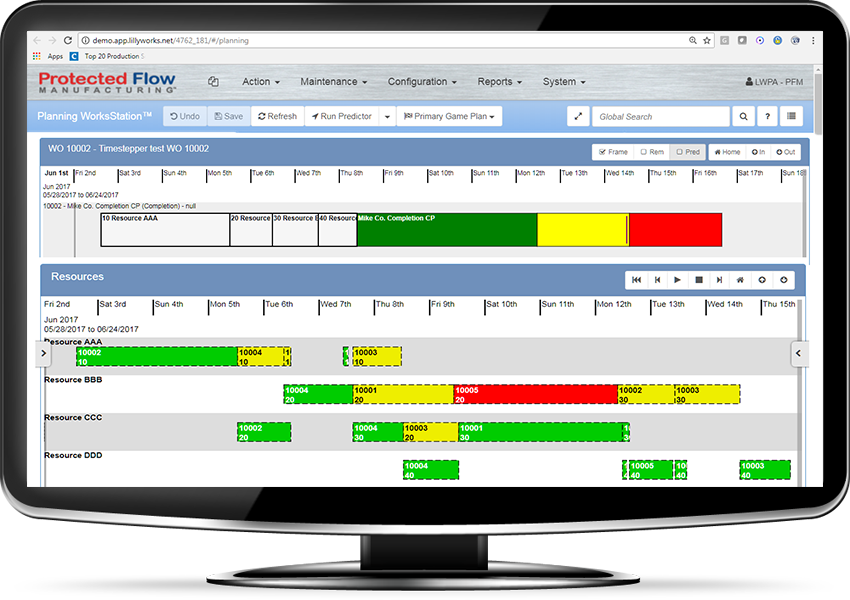
Proper Pacing to Prevent Bottlenecks
Putting materials into WIP too soon causes more problems than it solves. Instead of speeding up production, excessive WIP causes traffic jams in workflows and increases the risk of lateness. PFM keeps WIP at “just right” levels to keep things flowing smoothly and boost OTD. Users typically reduce WIP at least 20-30% in the first 6-8 weeks.
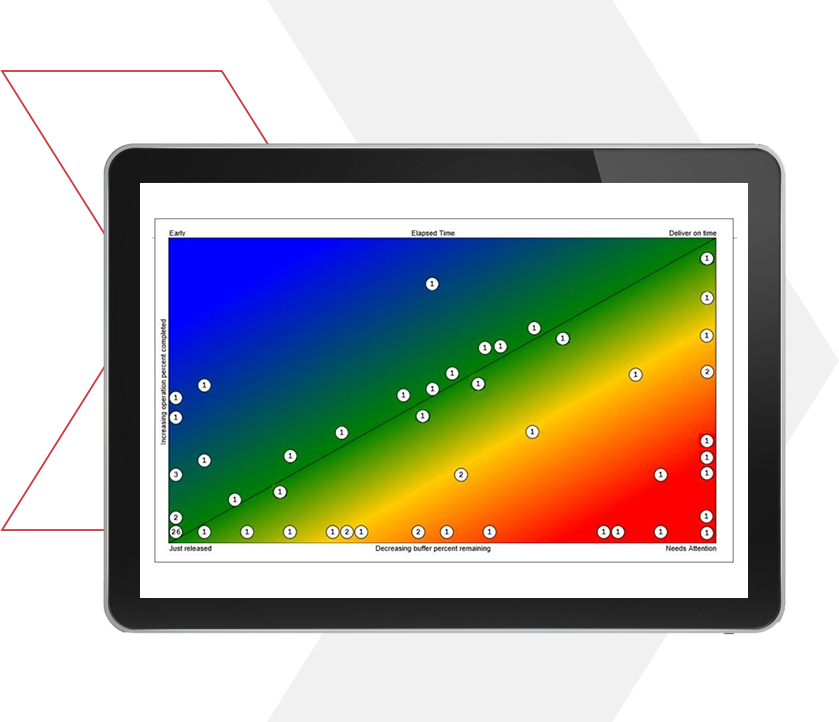
Predictive Prioritization with Proprietary Analytics
Traditional production scheduling software assigns future capacity to jobs. It must be re-run over and over as unplanned events happen. PFM simulates the use of your capacity and shows you what jobs are predicted to have problems and where these problems may occur. With a clear picture of the future, you can implement an action plan to deliver ALL jobs on time.
Aerospace & Defense
- Engineering with CAD integration
- Engineering change control
- Specifications and data "flow down" for ITAR, DFAR, etc.
- Actual job costing
- Project Management with Earned Value Management and milestone reporting
Automotive Manufacturing
- Configuration management
- Serial and lot control
- Design and engineering
- Capacity planning & scheduling (Lean, TOC, JIT)
- Actual costing
Electronics & High-Tech
- Alternate item on bill of materials (BOM)
- Item cross reference (supplier and manufacturer)
- Approved vendors and manufacturer lists
- Supply chain visibility with Web based portals
- Reference designators
Oil & Gas
- Strengthen Your Supply Chain
- Sophisticated Project Management
- Connect Service Efforts to Operations
- Localization & Financial Accounting Visibility
Field Service, Maintenance & Repair
- Improve Customer Satisfaction & First Time Fix Rate
- Reduce Days Sales Outstanding (DSO)
- Optimize Routing of Field Service Techs
- Support for Depot Repair, Break-Fix & More
- Offer Managed Service Contracts
Furniture & Fixtures
- Industry Expert Partners
- Increase Quote Win Rate
- Improve Planning & Scheduling
- Cut Operational Costs
- Shorten Product Development Lifecycles
Industrial Machinery & Equipment
- Win More Business
- Meet Customer Delivery Expectations
- Increase Velocity of Spare Part Sales
- Collaborate With Suppliers & Customers
- Leave Your Competitors Behind
Industrial Manufacturing
- End-to-end customer relationship, sales, purchasing, performance, and financial management
- Estimating with multiple quantity breaks
- Integrated capacity planning (Lean, TOC, JIT) with unlimited "what-if" scenarios
- Material planning with real-time visibility of demand and supply
- Cost control (actual, average, standard)
Medical Device Manufacturing
- End-to-end customer relationship, sales, purchasing, performance, and financial management
- Estimating with multiple quantity breaks
- Integrated capacity planning (Lean, TOC, JIT) with unlimited "what-if" scenarios
- Material planning with real-time visibility of demand and supply
- Cost control (actual, average, standard)
Metal, Glass, & Plastic Fabrication
- Purpose-Built ERP
- Estimate with Confidence
- Improve Delivery Performance
- Paperless Real-Time Shop Floor Data Collection
- The Right Materials at the Right Time
Process Manufacturing
- Tailor-make your formulations for maximum efficiency
- QC activities management with industry-aligned compliance labeling & reports
- Precision control over batch production, including by-products
- Define and monitor losses at each stage
- Dynamic ingredient adjustment to meet product objectives
Related Products and Services
- Seamless Integration
- Easy To Set Up. Easy to Maintain
- PFM Anticipates Issues
- See the Future Before it Happens
- Large & Small Jobs Are Optimized
- Create Efficiency and Reduce Lead Time
- Promote Visibility and Accountability Across Teams
- Switch From a “Push” to a “Pull” System
- Align ERP features with Your Shop Floor Systems
- Accurate Schedule and Production Dispatch
- Insight into Current and Future Capacity and Constraints
- Production Flexibility and Efficiency
- Knowledgeable and Self-Reliant Employees
- 40% - 60% On-time Delivery Improvement
- 15% - 40% Inventory Reduction
- 20% to 45% Shop Floor Productivity Gains
- 15% to 30% Lead Time Reduction
- 40% - 80% WIP Reduction
- Improve Manufacturing Efficiency
- Reduce Production Waste
- Track & Analyze Downtime in Real-time
- Instant Notifications for Shop Floor Workers
- Improve Operator Engagement & Communication
- Organize your data by time period
- Drill down to see detail of summarized or grouped data
- Easy filtering tools
- Self-service reporting means reports when you want them not when a report writer can get to them
- Real time Dashboards, Pivots, Reports, Charts with automatic drill downs
- Scheduling That Actually Works
- Expedited Quote to Cash
- Eliminate Future Issues
- Dynamic Material Planning
- Quick Implementation
- Looking directly at real time consumption rates of material rather than a static forecast
- Dynamically adjusting stock levels as demand changes
- Analyzing and suggesting stocking levels between manufacturing assemblies and sub-assemblies to optimize flow and eliminate stock-outs
- Managing procurement to align supply dynamically with changes in demand